Cone crusher is a kind of medium and fine crushing equipment, which is suitable for processing medium hardness and high hardness stone. In recent years, because of its technological innovation, convenient operation, reliable and safe advantages, it is very popular among users. At the same time, with the continuous development of mining technology, cone crushers are divided into single-cylinder, multi -cylinder, full hydraulic, symons and spring types. So what are the differences between single-cylinder cone crusher and multi -cylinder cone crusher?
The multi -cylinder cone crusher has six parts: ① lower frame part② eccentric sleeve part ③ transmission part ④ support sleeve part ⑤ adjusting ring⑥ moving cone
Ⅱ. Working Principle
Single-cylinder cone crusher: after the material enters into the crushing chamber, the spindle assembly rotates slowly in the eccentric copper sleeve under the resistance of the material, and the running track of the inner cone seems to swing back and forth in the crushing chamber. At the same time, the material is crushed by the swinging inner cone, and the connection between the support sleeve and the frame body is pressed by the hydraulic cylinder. When the crusher falls into the metal block and other indestructible objects, the hydraulic piston at the bottom will lift the moving cone of the single-cylinder, which can adjust the discharge port, protect the iron overload and eliminate the blockage
Multi -cylinder cone crusher: after the material enters the crushing cavity from the feeding port, it is crushed by the mutual impact of eccentric shaft and rolled mortar wall. The hydraulic safety system can eliminate the fault from the support sleeve and fixed cone by hydraulic pressure when the machine has iron fault or stuffy car. It has good safety function, greatly reduces the maintenance rate and improves the efficiency.
Ⅲ. Performance
single-cylinder hydraulic cone crusher: ① it integrates mechanical, hydraulic, electrical and intelligent control technology, representing higher crusher technology; ② through the design structure of single-cylinder at the bottom, it completes three important functions of directly adjusting the discharge port, preventing excessive iron and cleaning the cavity; ③ PLC + touch screen full-automatic control system, ensuring the safe operation of the equipment; ③ the design of single cylinder at the bottom of the hydraulic cone crusher can ensure the safe operation of the equipment;
multi -cylinder hydraulic cone crusher: ① fixed shaft structure design, large crushing force, low energy consumption, less investment in equipment foundation; (2) crushing chamber is divided into medium crushing, medium crushing, fine crushing and very fine crushing according to crushing particle size requirements; (3) crushing chamber shape can be arbitrarily changed from standard super coarse chamber shape to short head ultra-fine chamber shape to meet the requirements of large-scale product particle size;
Ⅴ. Crushing Effect
The results show that the content of fine material under the discharge port of multi-cylinder cone crusher is high, the crushing effect is better, and the layered crushing effect is better; but the crushing effect of single-cylinder hydraulic cone crusher is better, and the carrying capacity is large.
Ⅵ. Output Size
The upper and lower ends of the single-cylinder cone crusher spindle are supported, which can bear greater crushing force and stroke. In addition, the special crushing cavity shape adapted to the lamination principle makes the machine have higher crushing efficiency.
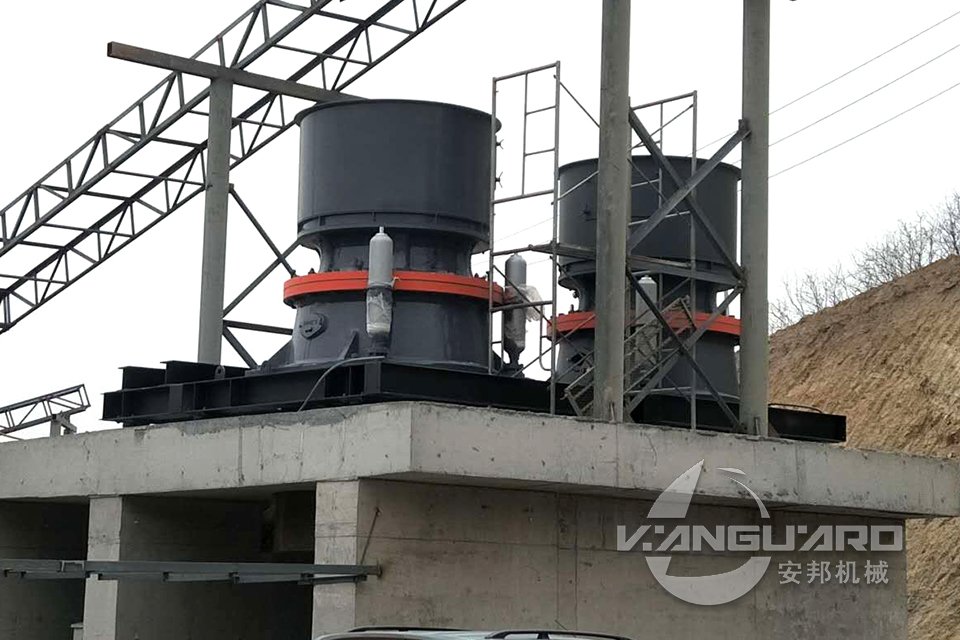
Ⅰ. Structure
The structure of single-cylinder cone crusher is mainly divided into upper frame assembly, lower frame assembly, moving cone assembly, transmission shaft assembly, eccentric sleeve assembly and hydraulic cylinder assembly. Its auxiliary components are composed of electrical system and thin oil lubrication system. The multi -cylinder cone crusher has six parts: ① lower frame part② eccentric sleeve part ③ transmission part ④ support sleeve part ⑤ adjusting ring⑥ moving cone
Ⅱ. Working Principle
Single-cylinder cone crusher: after the material enters into the crushing chamber, the spindle assembly rotates slowly in the eccentric copper sleeve under the resistance of the material, and the running track of the inner cone seems to swing back and forth in the crushing chamber. At the same time, the material is crushed by the swinging inner cone, and the connection between the support sleeve and the frame body is pressed by the hydraulic cylinder. When the crusher falls into the metal block and other indestructible objects, the hydraulic piston at the bottom will lift the moving cone of the single-cylinder, which can adjust the discharge port, protect the iron overload and eliminate the blockage
Multi -cylinder cone crusher: after the material enters the crushing cavity from the feeding port, it is crushed by the mutual impact of eccentric shaft and rolled mortar wall. The hydraulic safety system can eliminate the fault from the support sleeve and fixed cone by hydraulic pressure when the machine has iron fault or stuffy car. It has good safety function, greatly reduces the maintenance rate and improves the efficiency.
Ⅲ. Performance
single-cylinder hydraulic cone crusher: ① it integrates mechanical, hydraulic, electrical and intelligent control technology, representing higher crusher technology; ② through the design structure of single-cylinder at the bottom, it completes three important functions of directly adjusting the discharge port, preventing excessive iron and cleaning the cavity; ③ PLC + touch screen full-automatic control system, ensuring the safe operation of the equipment; ③ the design of single cylinder at the bottom of the hydraulic cone crusher can ensure the safe operation of the equipment;
multi -cylinder hydraulic cone crusher: ① fixed shaft structure design, large crushing force, low energy consumption, less investment in equipment foundation; (2) crushing chamber is divided into medium crushing, medium crushing, fine crushing and very fine crushing according to crushing particle size requirements; (3) crushing chamber shape can be arbitrarily changed from standard super coarse chamber shape to short head ultra-fine chamber shape to meet the requirements of large-scale product particle size;

Ⅳ. Feed and discharge particle size
The feed size of single-cylinder cone crusher is larger, and the feed size is less than 560 mm; the feed size of multi -cylinder cone machine is smaller, and the feed size is less than 326 mm; For single-cylinder cone crusher, the size of the discharge port is adjusted by the hydraulic cylinder at the bottom of the machine driving the crushing wall up and down, and the size of the discharge port is 6-41mm; for multiple-cylinder cone crusher, the size of the discharge port is adjusted by pushing the cylinder, and the discharge size is 8-51mm Ⅴ. Crushing Effect
The results show that the content of fine material under the discharge port of multi-cylinder cone crusher is high, the crushing effect is better, and the layered crushing effect is better; but the crushing effect of single-cylinder hydraulic cone crusher is better, and the carrying capacity is large.
Ⅵ. Output Size
The upper and lower ends of the single-cylinder cone crusher spindle are supported, which can bear greater crushing force and stroke. In addition, the special crushing cavity shape adapted to the lamination principle makes the machine have higher crushing efficiency.