Both jaw crusher and gyratory crusher are commonly used as primary crusher. The jaw crusher is more widely used, which may be because of price factors. Besides, there are big differences between the two in terms of appearance structure, production capacity, process design, energy consumption, maintenance, etc. The differences between them will be analyzed in detail below.
Comparison of advantages and disadvantages of jaw crusher and gyratory crusher in primary crushing:
1. Appearance structure
Jaw crusher
Simple structure, less cost, low machine height for easily configuring, convenient for maintenance
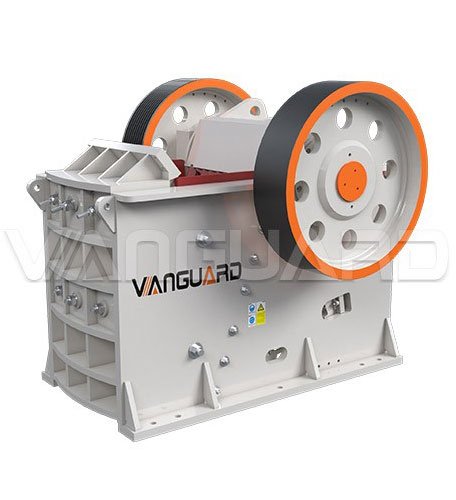
Gyratory crusher
Complex structure, high and large machine body which requires a quite high plant, higher infrastructure investment, heavy weight makes it inconvenient to transport.
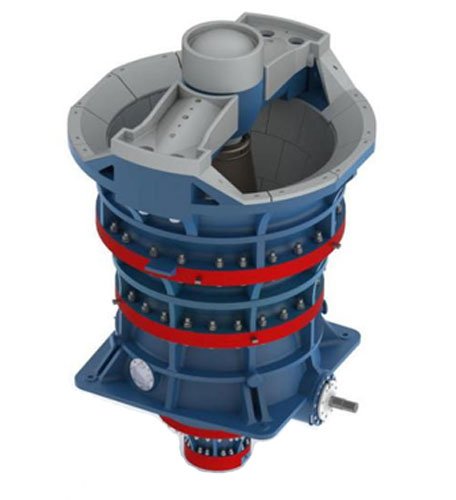
2. Working principle
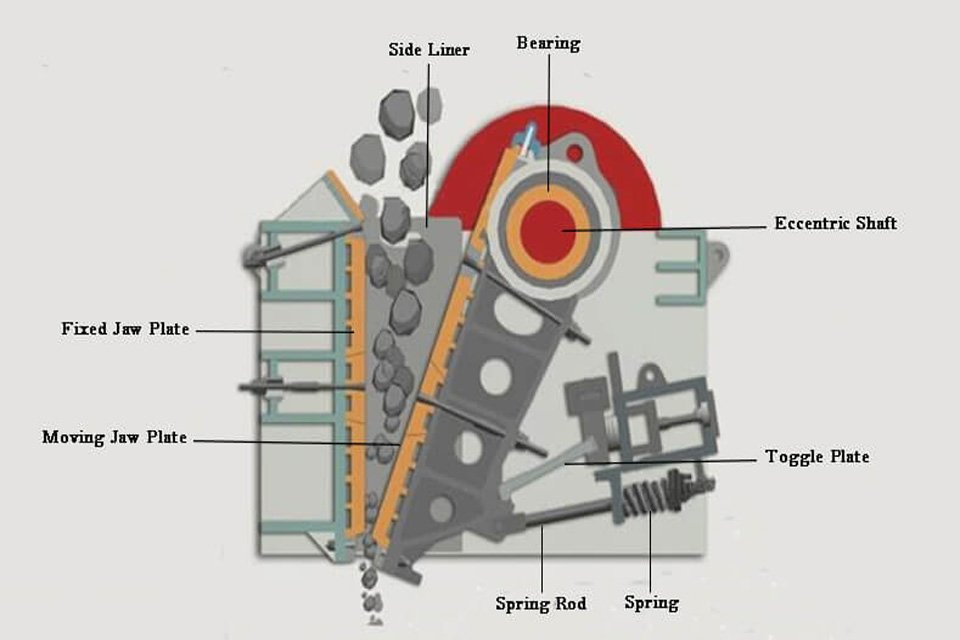
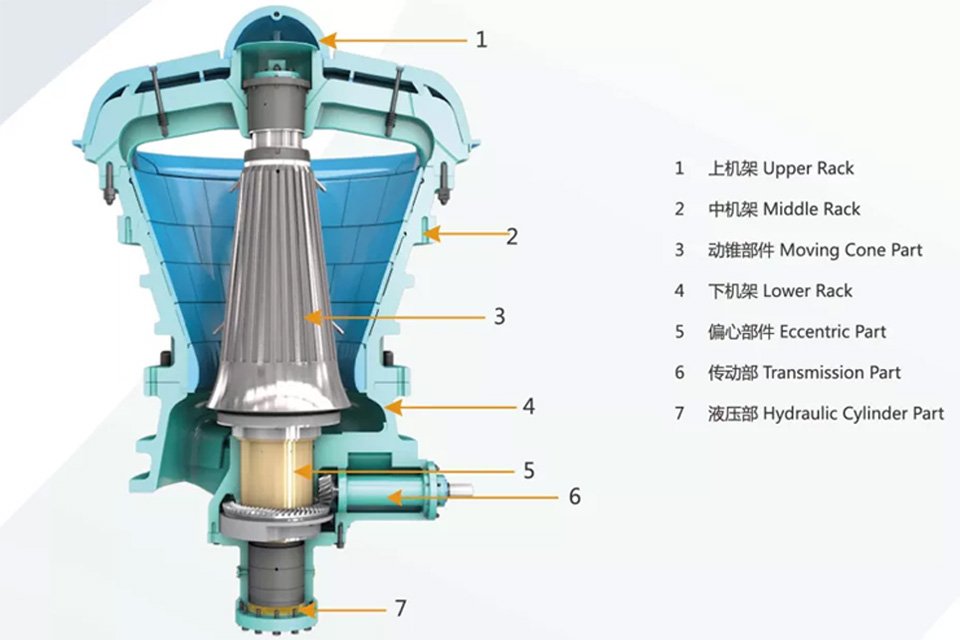
The structure of the jaw crusher mainly includes the frame, the eccentric shaft, the large pulley, the flywheel, the side guard plate, the toggle plate, the toggle plate rear seat, the clearance screw, the return spring, the fixed jaw plate and the movable jaw plate and other components.
The crushing method of jaw crusher is curved extrusion type. The motor drives the belt and pulley, and the movable jaw moves up and down through the eccentric shaft. When the moving jaw rises, the angle between the toggle plate and the moving jaw becomes larger, which pushes the moving jaw plate to approach the fixed jaw plate, and at the same time the material is crushed by multiple crushing, rubbing, and grinding; When the moving jaw descends, the angle between the toggle plate and the moving jaw becomes smaller, and the moving jaw plate leaves the fixed jaw plate under the action of the pull rod and spring. At this time, the crushed materials are discharged from the lower mouth of the crushing cavity. With the continuous rotation of the motor, the crushing mobile jaw is periodically crushed and discharged to realize mass production
The gyratory crusher is mainly composed of the beam part, the upper, middle and lower frame part, the movable cone part, the eccentric sleeve part, the transmission part and the hydraulic cylinder part.
When the crusher works, the horizontal shaft is driven by motor, which drives the eccentric sleeve to rotate through the gear, and then the eccentric sleeve drives the cone to swing in a circle, so as to achieve continuous crushing stones.
The size of the discharge port can be changed by adjusting the hydraulic cylinder at the bottom of the movable cone, which is convenient to adjust the product size; at the same time, the hydraulic cylinder also provides iron-over protection function. When an unbreakable object enters the crushing chamber, the hydraulic cylinder can automatically make the movable cone fall to release objects to protect the crusher.
3. Feeding and output sizes, capacity
Generally a feeder is needed before the jaw crusher, and the feeding requirements are strict. The large stones must be pre-crushed after blasting to meet the size of the jaw crusher. The output products are mostly flat, needle-shaped, sharp or triangular particles, with content can be up to 20%, and the product has a bad shape.
The crushing efficiency is relatively low because of intermittent crushing.
The feeding size of the gyratory crusher is large, and the output size is small and uniform. The finished material has a good shape, and the needle-like stone material is less than 10%. The raw ore can be poured directly into the feed port from the transportation tool without the feeder.
Continuous crushing, high capacity, large crushing ratio which can be 6-9.5, max up to 13.5. Stable work, low vibration.
The stones can be fed in any direction, and the material can be filled in the cavity with high crushing efficiency.
4. investment and economic benefits
Item | Jaw crusher | Gyratory crusher |
Wear parts life | Adopting the principle of impact squeeze crushing, the jaw plate wears quickly, and the maintenance workload is heavy. | Adopting the principle of lamination crushing between materials, the crushing process is continuously carried out along the circular crushing cavity, with uniform wear, and longer service life than jaw crusher wear parts. |
consumption | The coarse crushing process has high energy consumption. The jaw crushing adopts the principle of intermittent squeezing and crushing, and the single machine capacity is small. At present, the largest capacity of jaw crusher is only about 1,000 tons. A large production line needs to be equipped with multiple jaw crushers, and the output size of jaw crusher is not uniform and most of them are big, which increases the load of middle section crushing. | In a large production line, the energy consumption is much lower than large and medium-sized jaw crushers. |
Maintenance period | Due to the simple structure of the machine, the maintenance period is short, and the daily operation is simple | The structure is complex and the equipment price is high. The maintenance period is long and complicated. |
Mining cost | The mining cost is high. Due to the small feeding size of the jaw crushing, the drilling density is high, the explosive consumption is large, the large stones is more after blasting, and the crushing workload is large. | The mining cost is low. |
Applicable materials and occasions | It can crush ore with high moisture content, which is not easy to be blocked. Generally it is used as primary crusher by small concentrating mills and quarries. | It can be used as a primary crusher for various hardness stones, but it is not suitable for crushing viscous materials. Generally, the large concentrating mills use gyratory crushers. |
Dust pollution | The quantity of dust is large, and the large production line has many and scattered equipment, and it is difficult to completely seal it. That leads to poor working conditions and causes pollution to the environment. | One rotary crusher in a large production line can replace multiple jaw crushers, with less dust removal points and less dust . In addition, it can be directly watered at the feeding position to reduce dust, and the effect is better. |
Due to its high capacity and crushing ratio, generally the gyratory crusher is chosen by large concentrators as the primary crusher, except for viscous materials.
If measured from the aspects of feeding and discharging size and production rate, when both models can meet the requirements, it can be determined according to the medium and fine crushers used in the process flow, investment, infrastructure, and environmental protection.
According to experience, the clients can choose jaw crusher if one set crusher can meet their requirement, and change to gyratory crusher when more sets jaw crusher are needed.